RESEARCH
Facilities
Most of our research is performed in our own research facility, the Microlab.
The Microlab is equipped with some nice tools for investigating all kind of properies and behaviour of construction materials.
Some of the things we have are:
- servo-controlled systems for mechanical loading
- specimen preparation tools for impregnating, cutting, grinding, polishing and thin section making
- TGA, XRD, XRF, PSD, BET, MIP, ICP
- ESEM, Digital and optical microscopes
- ovens, CO2 curing cabinets, freeze-than chambers, ASR-reactors, RCM-testing, Adiabatic heat development, TSTM, ADTM.
- Creep-frames
- Rheometers
- Nano-indenter
- 3D printers at different scales.
Topics
Self-healing concrete
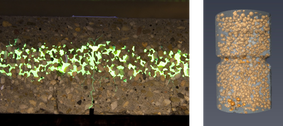
Cracking in conventional reinforced concrete is virtually unavoidable due to mechanical loading, early-age shrinkage, thermal effects, freeze-thaw, or a combination of these factors. Concrete with the ability to heal cracks by itself, therefore, have the prospect of exhibiting significantly improved structural and durability performance. To promote self-healing in concrete, extensive research has been carried out over the last decades either to stimulate the intrinsic/autogenous self-healing capacity of cementitious materials (e.g., via use of mineral additives, crystalline admixtures, or superabsorbent polymers) or to develop novel autonomous self-healing mechanisms (e.g., via the application of micro-, macro-, or vascular encapsulated polymers, minerals, or bacteria).
We are working on development and optimisation of various methods for self-healing both experimental as well as through modelling.
For the bacterial concrete that we developed a spin-off company was created:
3D concrete printing
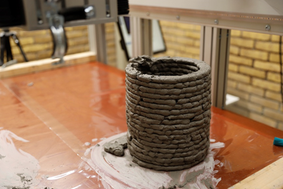
Three-dimensional concrete printing (3DCP) is one of the most common techniques of the
additive manufacturing (AM) for concrete, in which the cementitious material gets extruded layer upon layer, by a digitally controlled robot. This new construction technique makes it possible to structurally optimise the architectural design, resulting in more slender structures and more efficient use of the material. Additionally the technique potentially has economic benefits as it makes the use of formwork super uous. This can speed up the production process and reduces formwork costs. However, despite the benets that this additive manufactoring technique offers, it's not yet widely applied in practice, due to the multiple technical challenges that still need to be overcome.
We are working on development of new and green mixes for printing that also overcome the lack of tensile strength and deformation capacity. This is done by using special SHCC mixes for printing. We also add self-healing agents (www.smartincs.eu) to the printing material to make them more robust.
Delft Lattice Model
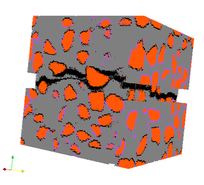
The use of lattice models like the Delft Lattice Model or similar discrete elements models like LDPM, spring or beam network models or peridynamic models have become more and more popular since this first publications 30 years ago. These type of models are often used as research tools to design or support experiments and to get insight into various fracture mechanism. While 30 years ago these models were limited to 2D, nowadays full 3D simulations on various scales are possible. Another feature that is added to these models is the possibility to perform diffusion or transport simulation using the same discrete elements or a coupled dual lattice mesh. This opens the possibilities to perform coupled transport and fracture simulations to study durability performance of concrete elements and structures.
We still use the models in various projects, also to simulate the process of 3D printing.
Furthermore we are developing a graphical user interface and option to simulate hardening concrete. For this have a look soon at www.femris.com.
Self-healing asphalt
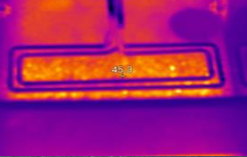
Porous asphalt, due to its advantages of noise reduction and water drainage, is widely used in the surface layer of the highway in the Netherlands. However, the porous structure makes it prone to ravelling, therefore more frequent maintenance and reconstruction than other asphalt mixtures The porous asphalt service life can be extended with self-healing technology, such as: induction heating and encapsulated rejuvenator.
We work on both methods and the combination of both. Furthermore we started a spin-off company that brings the technique to real applications. More info on this can be found at www.epionasphalt.com.
Durability mechanics
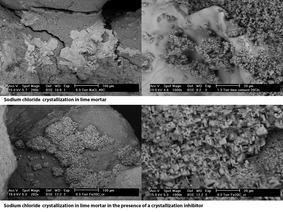
Properties and behaviour of construction materials changes in time due to ageing of the material, varying or changing environment and attack or ingress from outside.
These effects lead to physical or chemical changes in the material which often result in local deformation and stresses that cause damage.
Examples of mechanisms that we study are:
- extreme temperature changes at the surface of concrete
- salt crystallization in (lime) mortars
- chloride ingress and reinforcement corrosion.
- alkali silica reaction in concrete
- ageing of glue layers in glass applique
Early age concrete
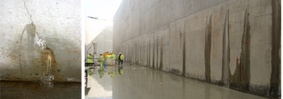
Early age cracking is a problem for massive concrete structures. A combination of hydration temperature, autogenous shrinkage, development of mechanical properties (strength, stiffness and visco-elastic properties) and finally restraining of deformations can lead to stresses in the young concrete that result in cracks. These cracks cause problems like leakage, durability and also structural capacity and safety of the structure.
The topic has been studied and reported in many articles. Furthermore finite element tools have been developed that can be used for the design of these structures.
Problematic however is are the properties during the first day of hydration, especially autogenous shrinkage (or expansion) and the visco-elastic properties. With the design of new experimental set-ups, finite element modelling and machine learning techniques we try to tackle the issue.
Micro-Mechanical Testing
A large part of the research we do in the Microlab deals with development of tests to charaterize micromechanical properties of materials. The properties are used to understand behaviour, but also as input and validation of our modeling activities. Often we combine the experimental techniques like nano-indentation, CT-scanning and small scale fracture testing with the simulations with our models. In the images below you can see some examples of fibre pull-out with tensile compression stage in ESEM, nano-indentation express test (in liquid) stiffness mapping, and micropillar compression test with nano-indenter observed in ESEM.
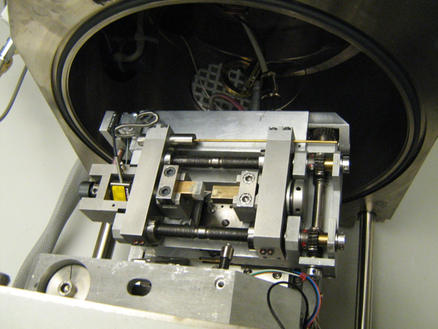
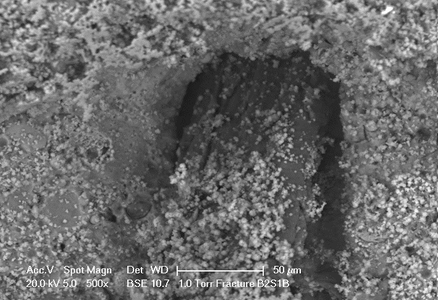
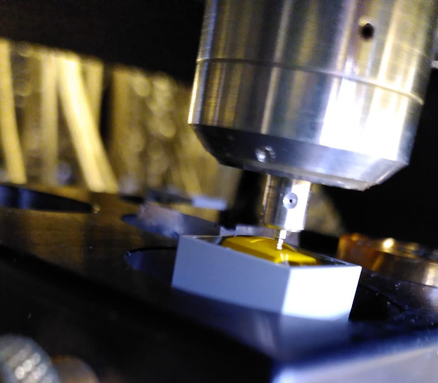
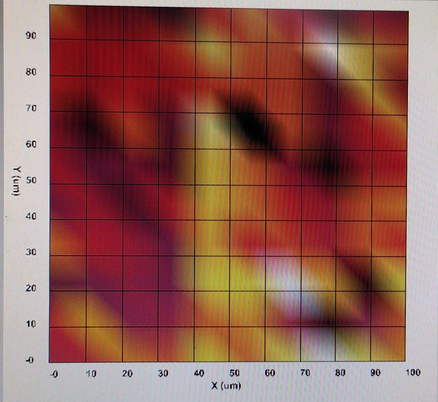
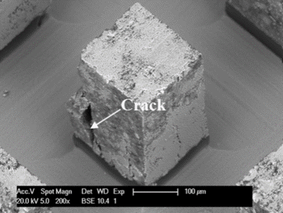
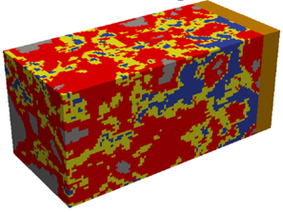
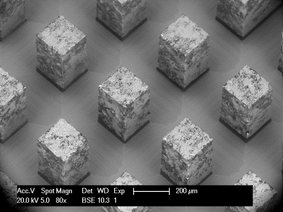